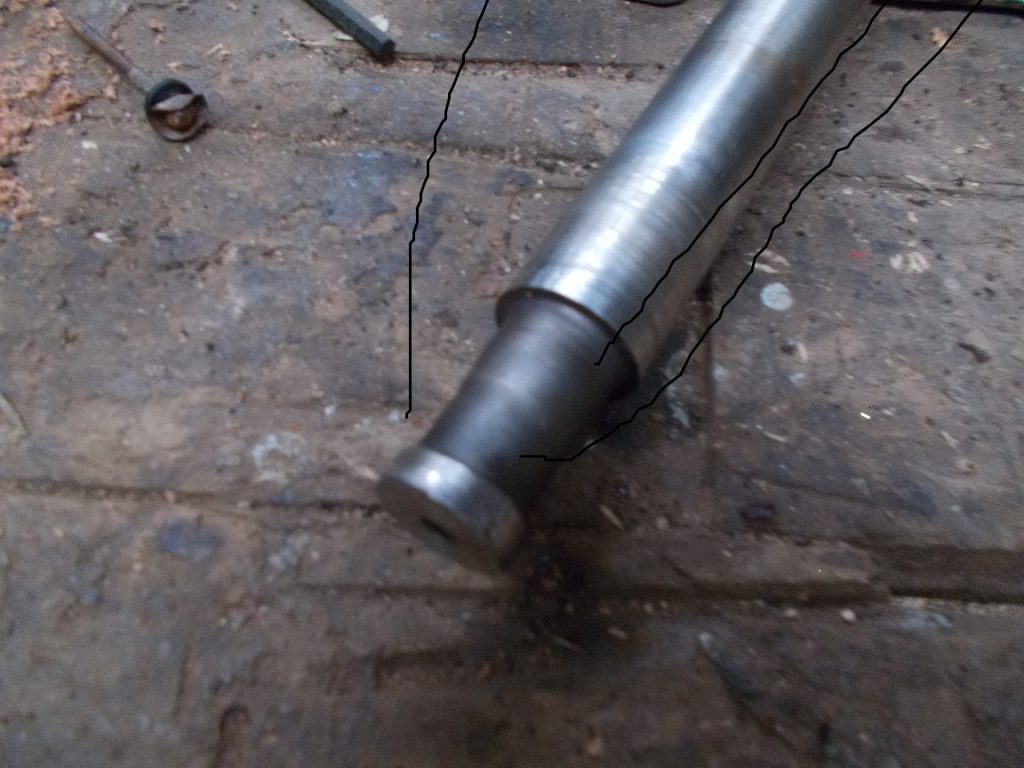
The hydro system is pretty well self-governing, and I don’t get down to the turbine/generator bit very often. I have a couple of indicator light bulbs to let me know what the power is and and where it is going that I can check at a glance as I walk by. So all has been good for a couple of months without attention so I decide it is about time for a bit of grease to the bearings. I get down there and all is humming nicely when I notice that there is a wobble on the shaft at one end. Oh bugger! I shut off the water supply and find one bearing has failed so the shaft started turning in the bearing and has worn away several mm of the shaft diameter and a few mm of the bearing inner ring.
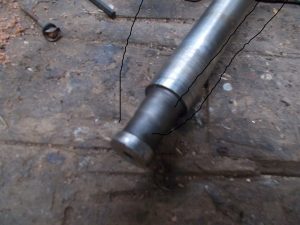
knackered shaft end
The shaft was flapping around with 5mm of clearance instead of a very tight fit. It doesn’t reduce the power output, and doesn’t show up at all on the indicator lights at the control center.
Which leads me to a historical note about the invention of the turbine type I am using called a ‘Pelton Wheel’. In about the early 20th century, an engineer called Mr Pelton was employed by a mining company operating in remote parts to provide electrical power for a mine. He had a similar problem to mine but where the bearing failure was catastrophic, completely severed one end of the shaft so that the turbine with buckets like deep bowls was skewed at a considerable angle to the incoming jet of water. His reaction was probably the same as mine. Oh bugger, lots of work here! But he noticed that to his consternation, it was actually producing more power. Totally stuffed, yet working better. WTF? A mechanic would have fixed it to how it had been before, but an engineer like Pelton had to know why. He realised that preserving the momentum of the water jet and smoothly guiding it round 180 degrees, doubled the amount of energy extracted from the water jet. The Pelton wheel is the most efficient engine known at over 90%.
That was for nerds, the rest of you can tune in again. So on Saturday I have to shut down the hydro. Murphy’s Law strikes again as it is 2 days before I can get parts. The shaft has to be rebuilt with the ground down end built up with welding beads of stainless steel, then turned down to exact size on a quality lathe so there is an interference fit of a few thousandths of a millimetre. I can’t bodge that bit. So early Monday morning I take the shaft to Atherton for a re-build. At this point I have to admit to a blunder. The bearings I took off were covered with grease and muck, so I got an old and clean one out of the drawer to take to town to buy new ones at the bearing shop. They looked at the numbers and gave me the exact same bearings. I went to the engineering company and told them to re-build the weld for this brand new bearing which I gave them, which they did excellently and in the same day. I got home and presented the bearings to the shaft, and it fitted like a brick in a shirt sleeve. What has gone wrong here?? After staring at the offending pieces of steel for a long time, it occurs to me to check sizes with my vernier gauge. The new machined end is exactly 1 inch. The other end is 25mm. A difference of 0.4mm. I had forgotten that 30 years ago I’d widened the turbine case to increase efficiency and installed a new longer metric shaft. I had grabbed an ancient bearing from the drawer of the old imperial size from the previous shaft.
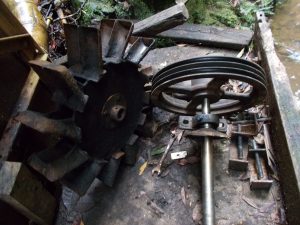
parts machined and ready for assembly
In the end all works well, except for the ugly fact I have one metric bearing and one imperial bearing on the same shaft. This is many orders of magnitude different from a similar balls-up of imperial and metric units that saw a 4 billion US dollar Mars lander crash because it actually though it was going to land 3km below the surface. It took an army of engineers and a host of committees to make that blunder. I did it all by myself. I was $65 out of pocket. Not even that really, as I have now got spare new bearings for each end.
Once I had the machined shaft and suitable custom bearings for each end, it only took me 3 hours to reassemble and put back on-line. But 5 days in all because it happened on a Saturday and there were only 3 metric self-aligning bearings in FNQ, so I had to wait on transport. In the mean time the system was kept going quite OK by the solar panels despite the fact there was a lot more cloud than sun. I did have a problem pulling the pulley wheel off the shaft with my gear pullers. In fact total failure. I had to carry the whole shaft assembly up the hill (several breathers on the way), to set up a circular anvil (the massive body of the old generator) to smash the shaft out of the pulley with a sledge hammer. A bit of good old-fashioned heavy engineering. It might surprise some people that I actually like doing this sort of shit. Especially at the end when I have won and defeated those obstinate chunks of metal.
I am stunned with admiration Mr. T. Thanks to Mr. Pelton, your substantial patience, your grim determination to beat the buggers, your engineering education, your fierce loyalty to DIY, your lateral thinking, and your strength of body and mind to complete the task, you did it!! If only I’d been born a male, had your education and experiences, your genes, your outlook, your mentality – then I could have defeated those obstinate chunks of metal too!