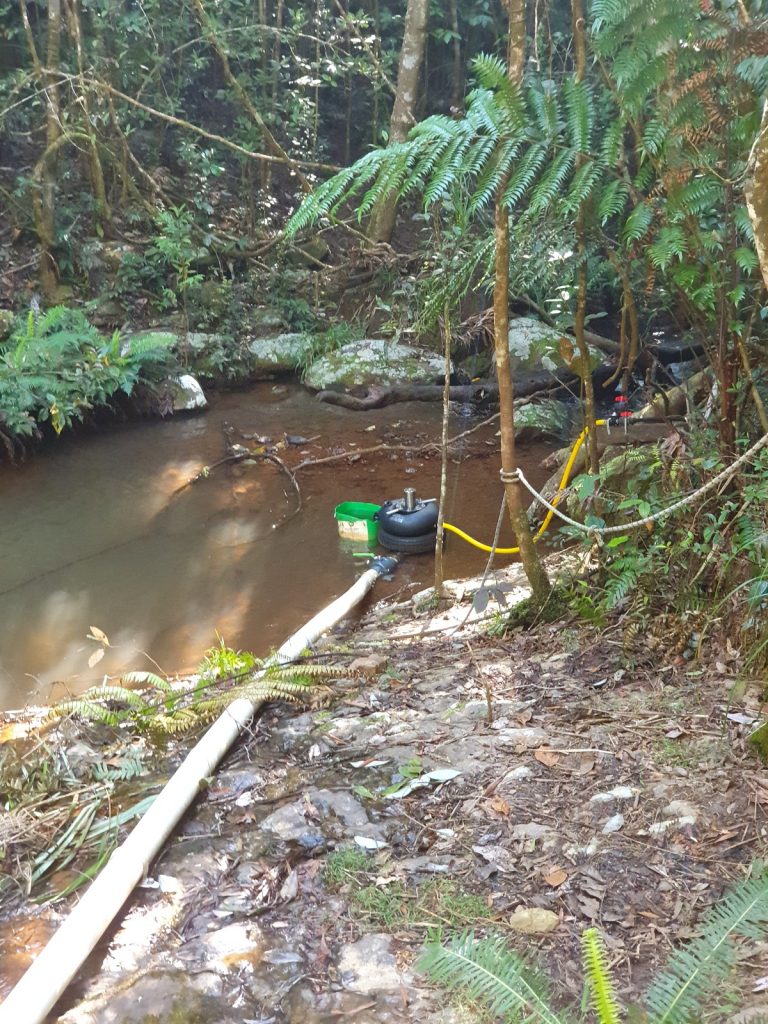
For the last 48 years I have been using several water driven ram pumps to provide water for Possum Valley. That is sufficient time to conclude that they can do the job, provide much more water than I need, cost nothing to run and are eco-friendly. But when something goes wrong, it can be expensive to fix at the local engineering works. On the down side, they are heavy, made of corrodable material like steel, are very sensitive to any solid matter, and make a lot of noise. A continuous bang bang at about heartbeat rate, which can be heard 100 m away. I dips me lid to the very ingenious French innovators, the Montgolfier brothers who invented it in the 18th century. Using a cannon ball as the ‘clapper valve’. Cannon balls were freely available then as Britain and France often exchanged them free of charge and at great velocity. But I digress. The ram pump also was very sensitive to even the tiniest of air bubbles that got in the drive pipe often by cracks or tiny holes due to pit corrosion. I have so often had to patch up the drive pipe with clamps and welding, but I can’t weld upside down lying in the creek, so I have to disconnect the pipes with meter long pipe wrenches and lug them to the workshop to weld. 75 mm steel pipes 9 m long are heavy when new, but get heavier when old with internal encrustation of rust and muddy gunk. And twice as heavy when two lengths are welded together. I’m getting too old for that shit.
So the new pump is 17 kg, requires low pressure 90 mm PVC pipe for the supply pipe and pumps twice as much as the ram pump. It is not sensitive to organic debris or a few bubbles. It can run at very low heads and flow rates to keep pumping in the dry season. If a cyclone torrent should trash the supply pipes, I can replace them with ease and little cost. There are no high stress parts that require re-engineering. What’s not to like? I am well satisfied with my new pump. It cannot be heard from more than 10 m away and it has a satisfying ‘gawoosh’ which blends in well with the ambient waterfall noise. I have installed a 75 mm ball valve on the supply pipe right next to the pump which can throttle the 4.5 m head and control the stroke rate. I use it as the ‘off’ switch and can set it partially open to get a stroke rate of 2 or 3 seconds as recommended by the designer.
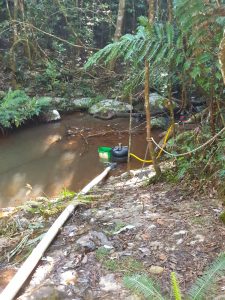
position in creek
I do not have direct feed from the weir, but use large diameter pipes (150 mm) going 25 m to convey the water to a header tank to have a double opportunity to filter debris out of the water. The header tank is double chamber to trap gravel that may come down in floods which happen just about every wet season. Now this may sound like a lot of clever design, but actually, I was just cobbling together junk that was lying about the place. The double chamber header tank is the body of a dead fridge/freezer lying on its back with a hole hacked between compartments so that gravel debris washed from the road should settle out in the first compartment. The supply pipe to this is some old stainless steel 150 mm chimney pipes and some 125 mm aluminium agricultural spray-line pipes I had laying around for a decade or two. Surprising what I can scare up when I go kicking piles of leaves. The final 25 m to the pump is 90 mm storm water PVC pipe which I actually had to buy. Cheap as chips. The inner tube above the car tyre is filled with water and is just a weight to shorten the time the top part drops down. You can see the piston at the top of it’s cycle. When the tyre below inflates, the top part with the cylinder rises and that is the pumping part of the cycle. It is unusual in that the piston stays still and the cylinder moves. There is an inlet pipe in the plastic bucket which has a few rocks to keep it from floating away.
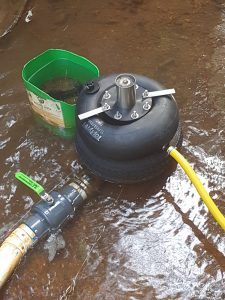
pump shut off
The fixing of the supply pipes did not go as smoothly as I had hoped. I did know that trying to find footing on a steep waterfall lubricated by layers of slime mold was going to be a challenge, but I didn’t anticipate the problems of drilling the holes for the rock bolts to anchor the supply pipe against floods. The rock was bloody hard and the tungsten carbide drills in a hammer drill were making feeble or no progress. It didn’t occur to me to sharpen the tungsten carbide edges, because I had often worked with percussion drill rigs when doing mineral exploration work. The drill bits are a flat plate, maybe 200 mm in diameter with balls of tungsten carbide protruding from the surface of tough steel. The down-hole hammer which moves less than a centimeter is driven at high speed by hydraulics from a 300 HP engine on the drill rig. It is a very brutal way of smashing your way through rocks hundreds of meters underground. So it took a while for me figure out that I needed to resharpen my modest little drill bit. Balls work if you have 300 HP to drive it, sharpening works if you have a feeble hand drill. I still shattered a couple of the carbide teeth and used a few bits, but I got the holes drilled. A couple of the the rock bolts were to anchor the pump. I don’t want to donate it to somebody in Innisfail when the floods come.
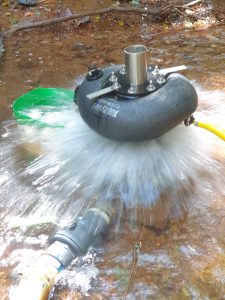
exhaust part of cycle
I did try to take a video of it working. Video works on the camera, but uploading to my computer only the sound track came through in the 13 sec clip, but the picture did not. So until I can find some IT guru to fix it, you will have to imagine the top half slowly rising in the pump phase, and then suddenly dropping with a fountain of water and a ga-woosh sound. Total cycle 2-3 secs.
hurrah, you are alive!
welcome back and another job well done.